Most people think of cables, wires or electronic boxes when they think of communications equipment, but there is also the mechanical element involved when it comes to transmitting data between the ground and the sky.
One of our customers sought us out with a number of mechanical requirements for a large, radar dish that was being designed. There wasn’t anything out of the ordinary about this radar engineering design, but it offered an opportunity to provide several of the wide variety of drive components we offer and work with the customer to help select the proper parts for his design.
The first area of consideration was the main drive for rotating the dish. This was to be servo controlled in order to provide precise positioning. Because of the low duty cycle and additional ratios down the line, we were able to suggest our Planetdrive series of economical servo gearheads. The 12 arc minutes of backlash were deemed adequate to meet the positioning parameters. Due to the low duty cycle, we were able to use the peak load capacity of the gearhead, which allowed downsizing, for significant cost savings.
The second component to be considered was the bull gear drive box. The dish assembly was to be mounted on a large bull gear, which was to be driven by a smaller pinion. This provided a high reduction ratio and additional mechanical advantage. A right-angle drive box was required because of the driveline configuration. We suggested our low-back Tandler spiral bevel gearbox product line. These provide both high strength and extremely precise motion for smooth rotation. The pinion drive gear was to be mounted directly on the output shaft. Radial load calculations were performed to be sure the pinion and bull gear separation forces did not exceed the bearing capacities.
The third component to be considered was an overload safety device to protect the drive system from an unexpected jam. Instead of using a standard shaft coupling to connect the jackshaft and input shaft of the spiral bevel gearbox, we selected an R+W integral coupling and torque limiter. These torque limiters come with a wide range of field adjustable torque settings and can be provided with four different re-engagement designs. In this case, we selected the single position re-engagement design so the predetermined programmable servo controls could quickly return to the home base. They also include a disengagement detection ring that can be read by a proximity sensor, which can alert a monitoring device to the overload.
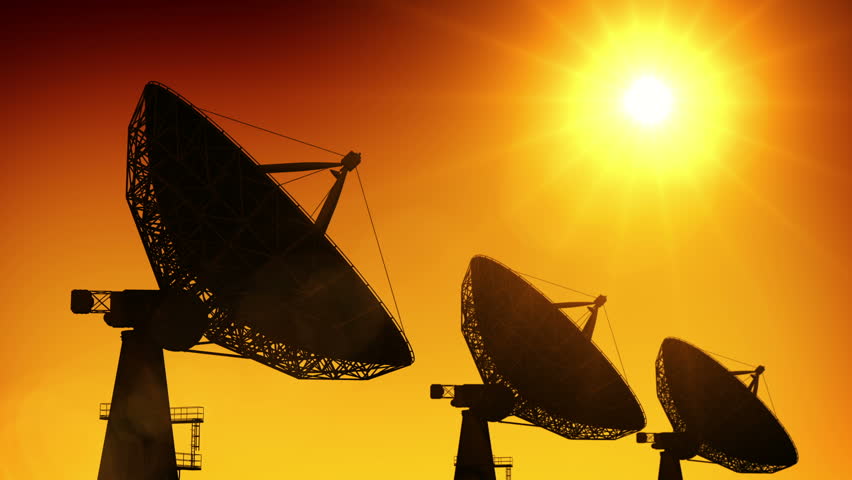
The fourth component to be considered was a drive mechanism assembly to adjust the angle of the dish. For this, we offered our industrial screw jacks product line. The basic design included a pivot bearing block mounted to the jack body to accommodate the varying angles. At the end of the screw, we provided a clevis attachment for connecting to a bracket at the radius of the dish. To drive the jack we flanged mounted a small Watt drive inline helical gear motor. Protection elements include a protection tube below the jack body, a protective boot above the jack body, and anti-rotation on the screw to eliminate any side forces on the screw-connecting bracket. A rotary encoder was attached to the gear motor to determine position.
The result of all this work was the ability of the customer to purchase all of the drive and safety components from a single supplier along with the engineering and service support to make the proper selections. This saved a tremendous amount of time and assured that all components would work in harmony.
DieQua partners with a lot of our customers specifying multiple drive components within a single system. This provides high value for our customers, and our consultative approach assures that the correct components, to maximize the performance of the machine, are selected.